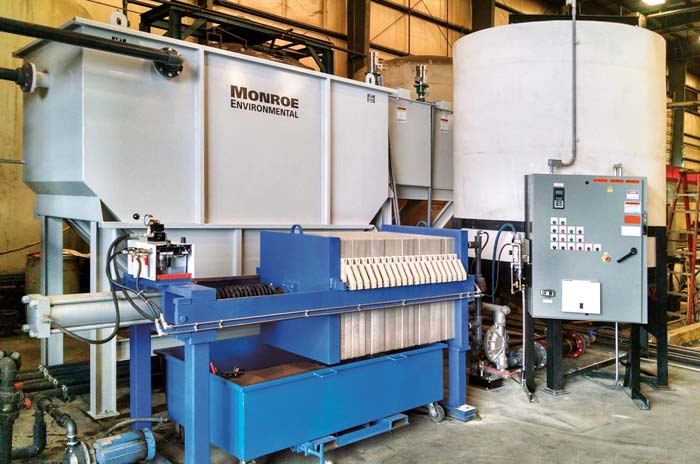
Monroe Horizontal Clarifier & Sludge Handling Package Improves Treatability & Lowers Cost
Challenge
A metal forming and stamping plant needed to upgrade its wastewater treatment system but had limited floor space. They wanted to reduce operation and maintenance costs while increasing the performance and versatility of treatment to remove solids, metals, and oils from an e–coating operation. The primary process goal was reduction of dissolved metals, but they also wanted to incorporate removal of oils from a secondary wastewater stream. The company sought the expertise of Monroe Environmental to assist with the upgrade.
Solution
Monroe evaluated the existing wastewater treatment system, made recommendations to reconfigure the layout, and custom engineered a solution specific to this client’s needs. Scope of supply included a Horizontal Clarifier with coated steel construction, separator plates, pipe skimmer, and pyramid sludge hopper; sludge holding tank with level controls; plate and frame filter press for sludge dewatering; and complete system piping, transfer pumps, and controls.
The Monroe Horizontal Clarifier was selected for its unique design and process advantages, which provided significant cost savings over traditional clarifiers. As one of the most versatile clarifiers available on the market, its unique parallel separator plate design effectively separates both settleable solids and floating materials. Used in combination with the dewatering equipment, the Horizontal Clarifier further reduced the amount of liquid in their end waste product, lowering disposal costs.
Result
The new equipment was able to efficiently process multiple wastewater streams as desired, and it produce a highly clarified effluent stream. The Monroe system also reduced maintenance and operational costs when compared to the previous operation which required manually emptying several holding tanks and hauling off the waste for treatment.
Monroe supplied a complete turnkey installation of the system, which was rated for a liquid flow rate of 50 GPM.