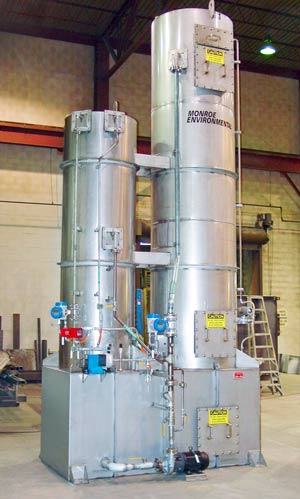
Sulfur Dioxide Scrubbing Using Caustic
Sulfur dioxide (SO2) is common in flue gasses from many combustion processes. As an example, we’ll consider a high temperature gas stream containing SO2 that leaves an incinerator or thermal oxidizer.
Typically, Monroe Environmental will provide a Quench Tower in a high temperature application such as this before a vertical counter-flow Packed Tower Scrubber. If solid particulate is present, a Venturi Scrubber may be employed to capture and remove PM prior to gas adsorption in the Packed Tower Scrubber.
Lowering the Temperature for Better Absorption
A temperature drop of the inlet stream from (800°F – 1,800°F) down to (140°F – 180°F) can be achieved with a Monroe Quench Tower. The quench tower has spray nozzles that add atomized water to the hot inlet gas stream to saturate it and lower the temperature by evaporative cooling. This lower temperature allows for the use of more cost-effective materials of construction within the Packed Tower Scrubber, and provides for better absorption of the gaseous SO2 by the recirculating NaOH and water scrubbing liquid.
The gas stream then enters the Packed Bed Scrubber. Here, the pH of the scrubbing liquid is monitored by a probe and typically maintained between 7.5 and 8.5 by a pH controller and chemical metering pump.
The basic reaction steps are as follows:
SO2 + H2O SO2H2O
SO2H2O + NaOH NaHSO3 (a salt) + H2O
NaHSO3 + NaOH Na2SO3 (a salt) + H2O (in the presence of excess NaOH)
NaOH neutralizes the absorbed SO2, producing a mixture of soluble sodium salts. The carefully chosen packing material provides a large surface area for reaction. The scrubbing liquid, SO2 in solution, and salts fall into the tank and are removed. The gas stream then passes through the moisture eliminator pad or chevrons in the top of the packed tower, which removes the remaining water droplets from the gas stream before it leaves the scrubber. Removal efficiency greater than 99% can be achieved.
Monroe Environmental has supplied numerous sulfur dioxide scrubbing systems for a variety of processes, including this Case Study exhausting a multiple hearth biosolids incinerator.